Ausgabe 3 · November 2006
Diesen Artikel als PDF
Lowrider und Packtaschen im Lowtech-Selbstbau
von Rainer Mai
Achtung, Nachbau nicht empfehlenswert. Hier geht es eher um authentische Folklore …
Als ich mich Anno 1984 anschickte, von Tunis nach Kapstadt zu fahren, hatte ich wohl an die 30 kg Gepäck (man gönnt sich ja sonst nichts ;o) an Bord meines Dreigangrads.
Das Problem
Hinten hatte ich Cannondale-Packtaschen auf dem normalen 80er-Jahre-Einfachgepäckträger. Diese Kombination hielt die 20.000-km-Tour, abgesehen von eher seltenen Näh- und Schweißarbeiten und dem täglichen Kampf mit den Reißverschlüssen, wacker durch.
Vorne dagegen gab es ständig Ärger. Auf dem Ebenfalls-80er-Jahre-Standard-Vordergepäckträger schaukelte, viel zu hoch und nicht wirklich stabil befestigt, eine Überwurf-Doppelpacktasche aus dünnem Kunstleder. Auch die, natürlich mit Schottenmuster, war damaliger Stand der Technik. Der PVC-Weichmacher gaste in der Saharasonne offenbar schnell aus, jedenfalls wurde sie bald spröde und bekam Risse, die immer wieder genäht wurden, bis die Tasche nach etwa 5.000 km nur noch aus bröckelnden Fetzen und Nähgarn bestand. Ich musste einen längeren Aufenthalt in Lomé (Togo) nutzen, besseren Ersatz zu beschaffen.
Die Alternative
An den Rädern britischer Trans-Afrika-Tourer sah ich zum ersten Mal die damals hierzulande noch unbekannten Lowrider: gute Konstruktion, wollte ich auch haben. Was bedeutete, einen zu bauen, samt den schon auf dem Wunschzettel stehenden »unkaputtbaren« und wasserdichten Packtaschen.
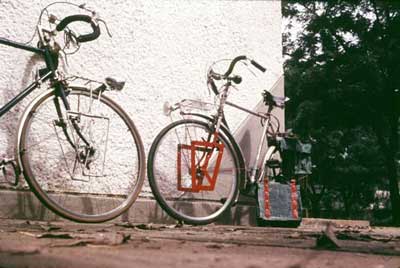
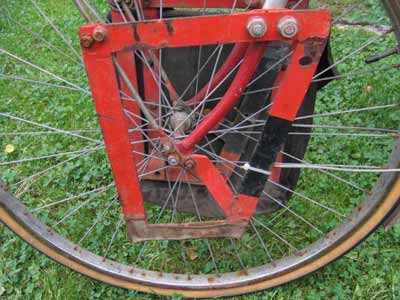
Stahlbau
Den Träger baute ich in einer Schlosserei unter freiem Himmel, aus Schrottmaterial und mit dem verfügbaren Werkzeug. Eisensäge, Feile und Bohrer (samt elektrischer Bohrmaschine) waren zwar vorhanden. Trotzdem kostete es viele schweißtreibende Stunden, bis ich das Material zurechtgeschnitten und ein paar Löcher reingebohrt hatte, weil alle Werkzeuge stumpf oder sonstwie zerschlissen waren. Die Stahlblechprofile, 3 cm breit und 3 mm dick, ließ ich zu Rahmen zusammenschweißen, die sehr schwer, aber dafür auch wirklich schwer zerstörbar sind. Die Befestigung an der Gabel erfolgte oben mit verbreiterten Seilklemmen (M10, es sollte ja was aushalten ;o), am Ausfallende über einen Stahlblechausleger passenden Kalibers und zusätzlich mit kleineren Seilklemmen am vorhandenen Hochgepäckträger, was diesen aussteifte und vor Bruch schützte.
Der Stoff
Den Packtaschenstoff erstand ich in ortsüblicher Weise auf dem Markt. Die Auswahl war einfach, weil es nur ein robustes Gewebe gab. Das war knallgrün und wurde für LKW-Planen verwendet: Naturfaser, an Markisenstoff erinnernd, aber dicker, schwerer und entsprechend reißfest.
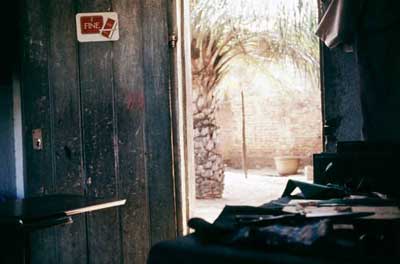
La Couture
Die Taschen hat ein Schneider in seiner bescheidenen Werkstatt mit einer HPSM (Human Powered Sewing-Machine) zusammengenäht, unter Mitwirkung ihres Konstrukteurs. Ich stellte nämlich fest, dass es nicht damit getan war, die Grundmaße vorzugeben. Sämtliche mathematischen und planerischen Operationen musste ich selbst durchführen, z. B. die Berechnung des Umfangs eines Rechtecks aus Länge und Breite, Materialzugaben für Säume … Taschen sind eben etwas anderes als aus Erfahrung auf den Leib geschneiderte Hemden. Und konstruktive Fähigkeiten, wozu etwa der Umgang mit Zahlen und zwei- wie dreidimensionales Vorstellungsvermögen gehört, scheinen in Afrika wenig verbreitet zu sein. Jedenfalls waren die Anwesenden immer wieder erstaunt, wenn nach meinen Maßvorgaben zum Schluss, oh Wunder, alles zusammenpasste … und weil wir grade schon am Nähen waren, gab es dann noch eine »Front Top Bag« für Federklappenbefestigung anstelle der nicht vorhandenen Lenkertasche und dazu das dringend benötigte Uhr-Armband.
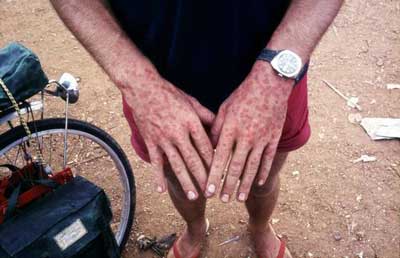
Das Holz
Die Rückwände entstanden aus Verpackungsabfall. Leider waren die verfügbaren »Zigarrenkistenbrettchen« zu klein, die Rückwände mussten aus mehreren mit entköpften Nägeln zusammengestiftet werden. Wegen der Wasserfestigkeit (im Tropenklima ist feuchtes Holz schnell biologisch abgebaut) lackierte ich sie besonders gründlich.
Zukunftsweisende Befestigung
Zur Befestigung am Träger verwendete ich durch die Rückwand geschraubte Stahlblechstreifen, die oben zu Haken gebogen waren. Das untere Ende des vorderen Streifens ist gekröpft, zum Einhängen in die Unterstrebe, um das lästige seitliche Pendeln (siehe auch den Beitrag von Rainer Rauschenberg) zu unterbinden. Das damals ebenfalls noch übliche Aushängen der Haken bei heftigen Stößen verhindert die vorstehende hintere obere Mutter, welche in eine Bohrung im Träger einrastet. Beide Features – Pendelstopp und Aushängsicherung statt Opas schlichtem Gummizughaken – definierten einen neuen Stand der Technik, den ich von Ortlieb erst etwa ein Jahrzehnt später geboten bekam – und das zunächst mechanisch weniger robust.
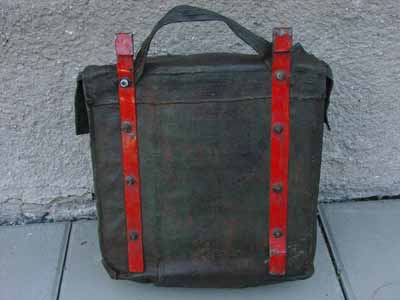
Olivax-Imprägnierung
Nun war der Träger montiert und lackiert und die Packtaschen im Prinzip fertig, noch Verschlussriemen mit Schnallen drangenäht … aber was tun gegen Wasser? Das Naturmaterial war sehr saugfähig, zumindest im Nahtbereich undicht und wäre unter diesen Umständen im Tropenwetter schnell verschimmelt. Als verfügbare Imprägnierstoffe fielen mir nur Olivenöl und Kerzenwachs ein. Das eine zu dünn, emulgierbar und damit auswaschgefährdet, das andere zu fest und zu spröde. Also mischte ich beides im Kochtopf, stellte experimentell eine halbtrocken-weichzähe Kalt-Viskosität ein, etwa wie bei Wachsjacken, und tränkte den Stoff gründlich mit diesem im heißen Zustand dünnflüssigen »Olivax«[tm].
Die Performance
Das Negative zuerst: Die zum Schluss noch eilig auf die Taschendeckel genähten, für den Schneider werbenden Logos »Fabriqué par Kassama, Togo« hielten leider nicht lange. Die Blechhaken der rechten Tasche bogen sich auf, bis ich sie endgültig am Träger festschraubte – was sich später im Alltagsbetrieb als sehr praktisch erwies: Die Packtasche samt Regen- und Werkzeug konnte ich nie vergessen, weil immer am Fahrzeug. Bei heißem Wetter schmolz das Olivax, die nassen Oberflächen nahmen Pistenstaub auf, bis die damit panierten Packtaschen (auf gut Englisch: the panniers ;o) nach ein paar Wochen ausreichend »getrocknet« waren.
Mit der so präparierten Maschine fuhr ich durch Zentral- und Ostafrika bis Kapstadt; dann wurde es von mir ein Jahr als Alltags- und Tourenrad benutzt, später zeitweise von verschiedenen Freunden. Die restlichen etwa 20 Jahre gammelte die Maschine teils in nassen Kellern, teils unter freiem Himmel vor sich hin. Die fest montierte rechte Packtasche hat all das mitgemacht; entsprechend mitgenommen sieht sie aus.
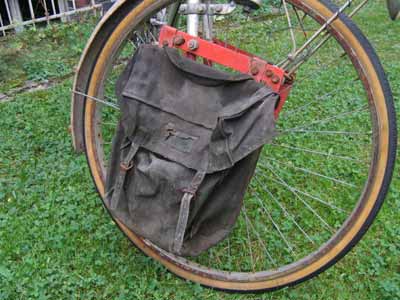
Die linke Tasche war insgesamt rund zwei Jahre und 20.000 Lastkilometer im Einsatz, wurde also eher »normal« benutzt. Sie scheint noch wasserdicht zu sein.
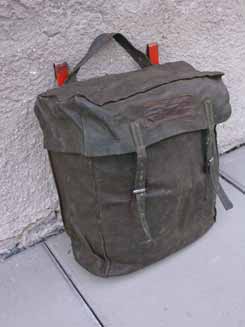
Insgesamt war ich rundum zufrieden: Taschen und Träger erwiesen sich nicht nur als schier »unkaputtbar« – im Unterschied etwa zu den zeitgenössischen Trägern von Blackburn und -Nachbauten, die gerne an der konstruktiven Sollbruchstelle versagten. Die Taschen waren meine ersten wirklich wasserdichten, was sie auf afrikanischen Straßen oft beweisen mussten: Tauchtiefe bis 15 Zentimeter, vorne große Bugwelle – und dabei der angenehme Gedanke, dass der Inhalt trotzdem absolut trocken bleibt. Das gab mir ein völlig neues Komfortgefühl. So machte Reisen Spaß, Lowtech sei Dank.
Zum Autor
Rainer Mai ist
Fahrrad-Sachverständiger in Frankfurt am Main, Maschinenbauingenieur,
Alltags- und Reiseradler, Mitgründer und Betreuer einer
Selbsthilfewerkstatt, Mitinitiator der »AG Verflixtes Schutzblech«.