Ausgabe 4 · November 2007
Diesen Artikel als PDF
Lowrider gleich Lowquality?
Lieber ohne »Sollbruchstelle« in den Urlaub …
von Stefan Buballa
Mit Rad und Campinggepäck eine Region zu erkunden ist ein besonderes Erlebnis. Bei der Wahl der Wege ist man/frau ebenso frei wie bei der Wahl der Tagesetappen. Ein lauer Sommerabend vor dem Zelt an einem kleinen See kann dabei DAS Highlight einer ganzen Radreise sein. Dieses Maß an Unabhängigkeit hat aber auch seinen Preis: Wie Kleidung, Zelt, Kocher und Schlafsack auf dem Rad so verstauen, daß das Handling nicht zu sehr leidet und auch kein Teil des Rades (z. B. die Speichen des Hinterrads) übermäßig belastet wird? Abenteuer möchte man/frau doch lieber mit den Bären (oder den Ameisen …) als mit der Fahrradtechnik erleben …
Die Theorie …
»Gewicht nach vorn« lautete schon in den 80ern die Devise von H.J.Zierke, die er in einem Artikel in »Radfahren« vertrat. Eine Gewichtsverteilung zwischen vorne und hinten von gar zwei Drittel zu ein Drittel sei – einen sinnvoll konstruierten Reiseradrahmen vorausgesetzt – optimal.
Jim Blackburn und die US-amerikanische Zeitschrift »Bicycling« führten eigene Untersuchungen zur optimalen Gepäckposition am Vorderrad durch und so haben sich bei Upright-Reiserädern schliesslich Lowrider durchgesetzt, um Gepäck vorne zu transportieren. Gehen wir von ca. 15–20 kg Bruttogepäckgewicht aus (inkl. Taschen etc.), kommen da schnell 10 kg allein für »vorne« zusammen.
… und die Praxis!
Aber halten die schicken und oft auch nicht gerade billigen Dinger überhaupt, was sie versprechen? Hierzu einige Erfahrungen des Autors:
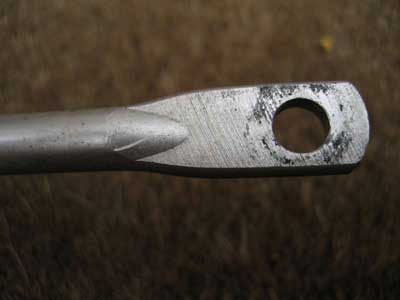
Auf einer meiner ersten Alpentouren macht es während eines langen Anstiegs plötzlich »knack« und auf der linken Seite sackt die Packtasche weg. Was war passiert? Bei meinem Lowrider von Bor Yueh (vgl. Bild 3) war nach nicht viel mehr als 1000 km mit Gepäck die Strebe, die den Unterrand des Trägers stützt, gebrochen. Und zwar genau unterhalb der Verschraubung (vgl. Bild 1). Im weiteren Verlauf trat der gleiche Defekt auch auf der Gegenseite auf! »Nun,« so dachte ich, »war ja nur Alu und überhaupt, diese Fernostnachbauten …«
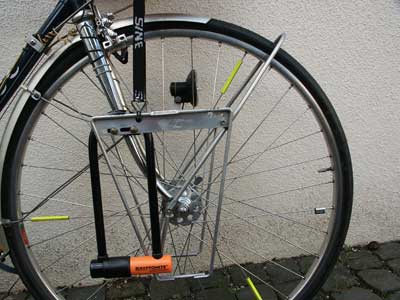
Von: Michael König
Also war ich hocherfreut, als ich erfuhr, daß es Ingenieuren gelungen war,
»das Rad neu zu erfinden« und ein (für Anfang der 90er) völlig neues
Lowrider-Konzept vorzustellen:
Der Träger bestand aus einem einzigen, gebogenen Rohr eines dünnwandigen
Vergütungsstahls, welches mehrfach mit sich selbst verlötet wurde. (vgl.
Bild 3) Geradezu sagenhafte Robustheit wurde diesem Träger in der
Fachpresse nachgesagt. Sogar den Transport von Passagieren würde er
klaglos überstehen und auch vom Hersteller Patria/Kleinebenne wurde er als
für höchste Belastungen (bis 20 kg) geeignet beworben.
So weit, so gut, das sagenhafte Teil wurde also zum stolzen Preis von fast 100 DM von mir gekauft und montiert. Auf einer längeren Radreise in Marokko belud ich ihn für eine Wüstenstrecke mit der maximalen Zuladung.
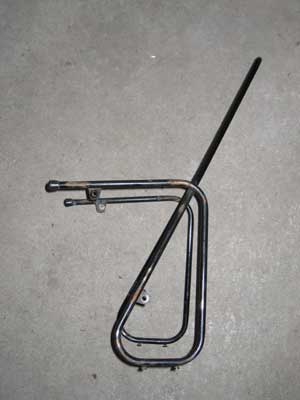
Von: Frank Brächter
Eine Inspektion nach einer besonders unebenen Piste brachte es ans
Licht:
Auf der einen Seite war die Unterstrebe komplett durchgebrochen, auf der
Gegenseite hatte sich der Riss bereits auf die Hälfte des Querschnitts
durchgearbeitet! So wie viele Jahre zuvor in den französischen Alpen hatte
sich der Defekt direkt unterhalb der unteren Verschraubung gebildet.
Ein freundlicher KFZ-Schlosser in der nächsten Oasenstadt behob den Schaden, in dem er ein langes Stück Armierungsstahl in die Rohrenden presste und den »achsoleichten« Träger mit seinem Elektroschweißgerät wieder zusammenfügte. Eine Reparatur übrigens, die hielt. Soweit also des Autors erste Erfahrungen mit Lowridern.
Ein wenig Konstruktionslehre …
Zwei Lowrider, unterschiedliche Belastungen, unterschiedliche Materialien … Hm, und eigentlich doch auch ganz unterschiedlich konstruiert, oder?
Nur auf den ersten Blick!
Auf den zweiten Blick gibt es einige Parallelen:
Bei beiden Modellen, wie auch bei den meisten anderen Lowridern auf dem
Markt sitzt die Tasche so tief, dass der untere Teil des Trägers keine
direkte Abstützung zur Gabel mehr haben kann. Von vorne betrachtet wird
eine weitere, im wahrsten Sinne fatale Gemeinsamkeit deutlich:
Es fehlt eine dreidimensionale Verstrebung, die über eine Art
Fachwerkkonstruktion das an der Strebe wirksame Biegemoment verringern
kann (vgl. Bild 4–6). Wenn man/frau sich nun weiterhin den Träger von
vorne betrachtet im Einsatz vorstellt, wird klar, das gerade die Region
unterhalb der Verschraubung großen Belastungen ausgesetzt ist.
Die Taschen schwingen während der Fahrt permanent aus und ein und biegen die Unterstrebe dabei hin und her. Nun ist der in dieser Schwingrichtung wirksame Querschnitt von der oberen Verschraubung des Trägers bis zur Unterkante desselben nicht derselbe.
Das obere »Teilstück« zwischen oberer und unterer Verschraubung wird durch die Gabel massiv ausgesteift, der untere, »freischwingende« Teil des Trägers setzt Verbiegung dagegen sehr viel weniger Widerstand entgegen. Und diese Änderung des wirksamen Querschnitts erfolgt nicht allmählich, sondern abrupt. Wo? Na, direkt an der unteren Verschraubung. Beide KonstrukteurInnen, die der deutschen FH genauso wie die aus Taiwan (bzw. aus den USA) haben damit in ihre Produkte eine ingenieurmäßige »Todsünde« eingebaut: Genau im Bereich der höchsten Dauerbiegebelastung entsteht ein sogenannter »Steifigkeitssprung«.
Abhilfe?!
Welche Kriterien sollte nun ein Lowrider erfüllen, um möglichst wenig bruchanfällig zu sein?
Zum einen kann man/frau natürlich den betroffenen Bereich verstärken. So hat oben genannter Patria-Lowrider alle nachfolgenden Strapazen klaglos durchgestanden, nachdem besagter maghrebinischer KFZ-Mechaniker das Zeugnis deutscher Wertarbeit und Ingenieurskunst praxisnah nachgearbeitet hatte.
Denkbar ist auch, den Durchmesser bzw. die Wandstärke der Unterstrebe zu erhöhen. Bei den meisten Aluminium-Modellen wird hier 8 mm Draht (Typ »Blackburn«), manchmal auch 10 × 1 mm oder 8 × 1 mm Rohr verwendet. Bei gängigen Stahlrohrlowrider kommen in der Regel Rohre der Abmessung 10 × 0,5 mm bzw. 10 × 1 mm zur Verwendung.
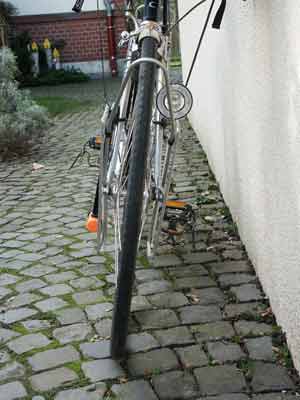
Von: Michael König
Eine weitere Möglichkeit der Verbesserung besteht darin, den Bereich der Unterstrebe dreidimensional mit einer Art Fachwerk so zu verstärken, daß sich die Belastung besser auf die ganze Länge der Strebe verteilt. Biegebelastung werden dabei im besten Fall ganz in Zug und Druckspannungen umgewandelt. Diesen kann das verwendeten Material besser widerstehen.
Schließlich kann man/frau aber auch die bruchanfällige Unterstrebe konstruktiv gleich ganz vermeiden und den Träger einfach etwas höher setzen. Netter Nebeneffekt: Auf Pisten mit tiefen Spurrillen oder bei hohen Bordsteinen setzen die Packtaschen nicht so schnell auf.
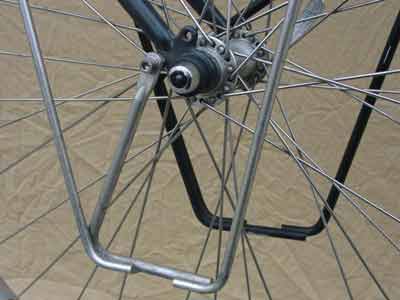
Von: Rainer Mai
»Ich kauf mir was …«
Diese Kriterien im Kopf habe ich mich auf dem Markt und an real existierenden Rädern umgeschaut und dabei wenig erfreuliches zu Tage gefördert. Der »Standard-Lowrider« hat immer noch das ursprüngliche »Blackburn«-Design – mit allen Schwachstellen wie dünner (8mm), biegebelasteter Unterstrebe, kantig gequetschten Enden derselben und großem Steifigkeitssprung. (vgl. Bild 2, 4–6)
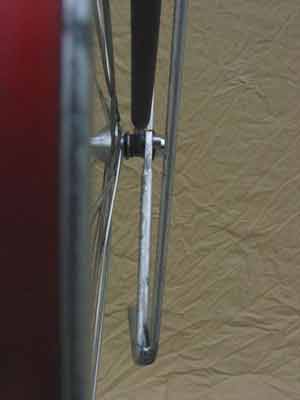
Von: Rainer Mai
Kurzzeitig waren auch Modelle von Blackburn auf dem Markt, bei welchen die Schwachstellen durch eine dünnwandige Stahlhülse »geschient« wurden.
Dies ist meiner Meinung nach wenig erfolgversprechend, da sich beide Materialien in Elastizitätsmodul, Streckgrenze und Dauerschwingfestigkeit stark unterscheiden und daher die Hülse keine zuverlässige Verstärkung der »Sollbruchstelle« sein kann. Erst bricht halt die gequetschte Strebe, dann die – überlastete – Hülse …
Interessanterweise geht es bei einem Modell vom Blackburn auch anders:
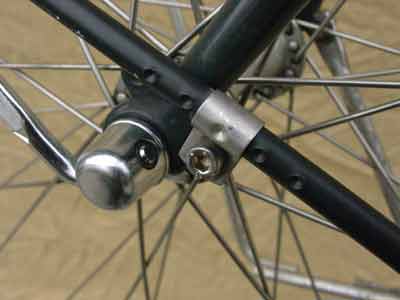
Von: Rainer Mai
Die Version ohne Bügel über dem Vorderrad hat an der unteren Verschraubung keine kantige Flachquetschung, sondern verwendet hier eine Schelle (vgl. Bild 7–8). Diese klemmt das volle Drahtmaterial, das zudem im vorderen Unterteil des Träger-Rahmens doppelt verläuft.
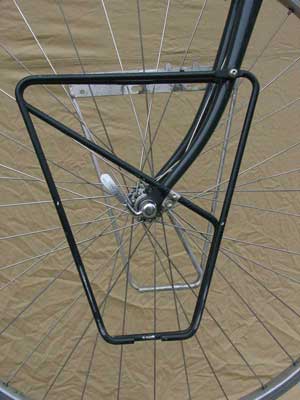
Von: Rainer Mai
Auf ähnliche Weise umgehen auch Träger von Zefal das Problem der Quetschung der Verschraubungsstelle.
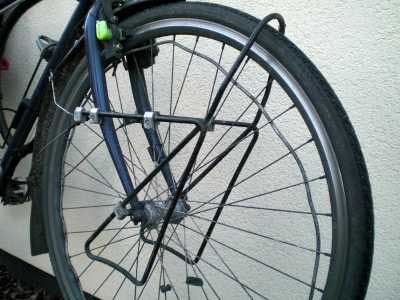
Von: Peter de Leuw
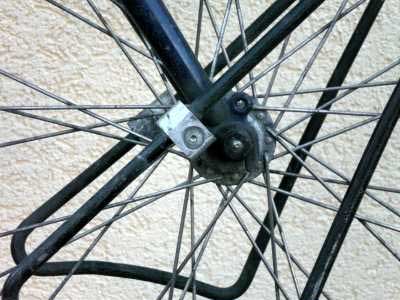
Von: Peter de Leuw
Auch der ESGE-Nachfolger SL vermeidet diese Schwachstelle an seinem Modell. Ob das bei Verwendung von 8 mm Aluminiumdraht allerdings reicht, die Bruchempfindlichkeit deutlich zu reduzieren?
Bei all diesen Modellen fehlt eine dreidimensionale Abstützung der Unterstrebe. Diese ist daher der vollen Biegebelastung ausgesetzt.
Es bleiben die diversen Hersteller von Trägern aus Stahlrohr. Die ehedem hochgelobten Patria-Lowrider (siehe oben) sind vom Markt verschwunden, was bleibt sonst noch? Gilles Berthoud stellt neben schicken Reiserädern und Retropacktaschen auch Gepäckträger her. Die Lowrider aus seiner Produktion ähnelten zeitweise denen von Patria: 25CrMo4 in 10 × 0,5 mm für die Unterstrebe, ohne weitere Verstärkung oder Versteifung. Bei hohen Belastungen scheint daher Vorsicht geboten.
Die aktuellen Modelle (verchromt) wirken z.T. robuster. Das Modell Adventure hat z. B. zwei Unterstreben und ein gute Konstruktion der unteren Verschraubung. Wie die meisten seiner Lowridertypen ist auch dieses Modell aber nur noch gemeinsam mit einem Reiseradrahmen erhältlich.
Vergleichbar konstruiert wie die Patria bzw. die ersten Tubus-Modelle sind auch die Träger von Stolz, einem kleinen Schweizer Hersteller. Es wird dort allerdings eine andere Stahlsorte verwendet.
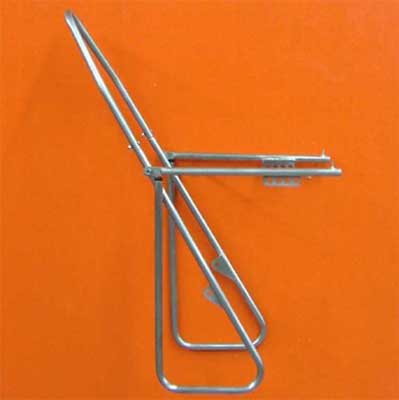
Von: Fahrradbau Stolz, Zürich
Bruce Gordon aus den USA baut Lowrider wieder etwas anders:
Hier trägt der Rahmen selber, er wird auf Achshöhe von einer Querstrebe gestützt. Auch hier fehlt eine dreidimensionale Abstützung nach innen, als Material kommt wieder 25CrMo4 in 10 × 0,5 mm zum Einsatz (vgl. Bild 13).
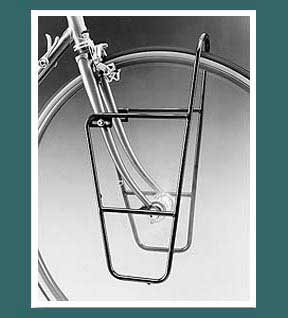
Von: Bruce Gordon
Als besonderes Highlight sei der sogenannte »High mount front rack« des Herstellers genannt: Durch »Höherlegen« gibt es keine bruchempfindliche Unterstrebe! Vom Handling her wird versucht, die Nachteile typischer Frontgepäckträger zu vermeiden, indem der Gepäckschwerpunkt näher an der Lenkachse liegt (vgl. Bild 14).
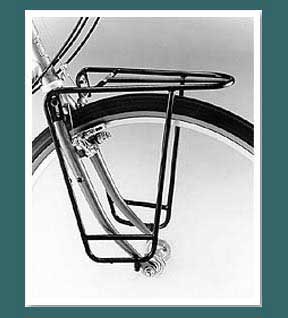
Von: Bruce Gordon
Und schließlich ist da noch TUBUS. Die Münsteraner haben bei den Lowridern kräftig Modellpflege betrieben: Ähnelten die ersten noch stark dem Kleinebenne Urmodell, so kam nach ein paar Jahren (und einigen Reklamationsfällen?) eine voluminöse Zusatzstrebe zum Einsatz. Diese bestand zuerst in einer eingeschraubten Aluminiumstrebe, dann wurde ein Stahlrohr fest eingefügt. Bei den aktuellen TARAs hat man/frau nun gleich den Durchmesser der Unterstrebe von 10 × 0,5 mm auf 14 × 0,8 mm erhöht (vgl. Bild 15–16).
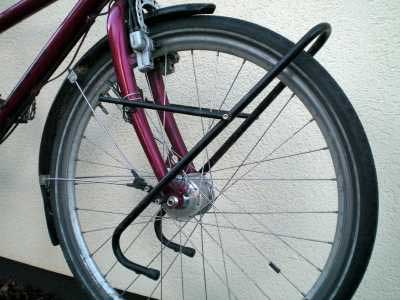
Von: Peter de Leuw
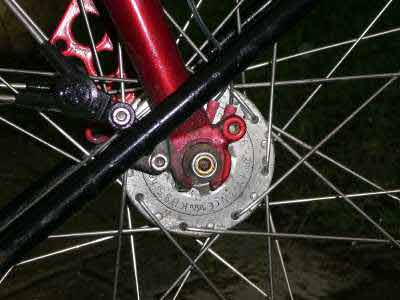
Von: Peter de Leuw
Do it …?
Bei der doch etwas beschränkten Auswahl sinnvoller, käuflicher Lösungen machte ich mich natürlich auch auf die Suche nach Verbesserungsmöglichkeiten in der heimischen Werkstatt.
Schon zu Zeiten der »Blackburn«-Monokultur haben findige BastlerInnen versucht, der flachgepressten »Sollbruchstelle« an der Unterstreben-Verschraubung die Anfälligkeit zu nehmen: Sorgfältig wurde die Presskante wegpoliert. Inwieweit dies wirklich geholfen hat, ist dem Autor nicht bekannt.
Aber auch »Katastrophenreparaturen« unterwegs (mit Armierungsstahl siehe oben oder Zelthering siehe unten) können sich als erstaunlich haltbares Edeltuning erweisen!
Reparatur unterwegs:
Demontieren, Plattklopfen des Endes an der Bruchstelle, neues Loch
reinmeißeln (oder bohren, wenn Bohrer in Reichweite), Zeltnagel als
Verstärkung parallel zu Fahrbahn und Fahrradlängsachse durchflechten,
das nimmt die Schwingungen auf.
Reparatur zu Hause – das lohnt sich, weil es danach hält:
Absägen, M8er Gewinde aufschneiden, Aluhülse mit M8er Innengewinde
aufschrauben, an M8er Schraube (Stahl! Baumarktqualität reicht) Kopf
absägen, heiß machen, platt klopfen, 5er Loch quer reinbohren, in andere
Seite der Hülse einschrauben, beide Schraubungen mit Epoxy-Kleber
festigen.
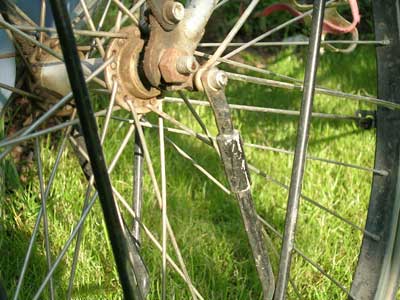
Von: Rainer H. Rauschenberg
Schliesslich kann man/frau auch gleich selbst zum Lötbrenner greifen und komplette Eigenkonstruktionen verwirklichen.
So wurde von Rainer Mai der ESGE-Stahl-Lowrider mittels eines Rohres 10 × 1 mm aus rostfreiem Stahl im Bereich der Unterstrebe 3-dimensional abgestützt, nachdem dieser unterwegs behelfsmässig ebenfalls mit einem Hering repariert wurde. Nun hält’s!
Bleibt der Selbstbau.
Wie dies auch in Afrika mit einfachen Mitteln zu bewerkstelligen ist, hat Rainer Mai in seinem Artikel Lowrider und Packtaschen im Lowtech-Selbstbau beschrieben.
Ich versuchte mich ebenfalls am Eigenbau, als es darum ging zum selbstgelöteten Reiseradrahmen passende, offroad-taugliche Lowrider zu finden. Bruce Gordons »High Mount Front Rack« war nicht erhältlich, von traditionellen Modellen war ich auf Grund leidvoller Erfahrungen nicht überzeugt (siehe oben) und auch TUBUS Modellpflege ließ noch zu wünschen übrig.
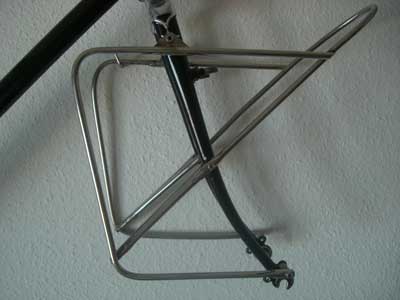
Heraus kam eine viel zu aufwändige Konstruktion aus rostfreiem Stahl, die zusätzlich über eine 3-dimensionale Abstützung des unteren Rahmens verfügte – bei einem »Highrider« wohl verzichtbar. Immerhin überstand er bis jetzt auch üble Pisten mit viel Gepäck ohne Probleme.
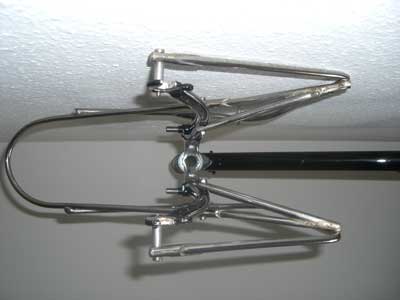
Deshalb zum Schluss, für alle, die es nicht lassen können, noch einige Tips zur Materialwahl und Verarbeitung:
Steif und leicht werden die Träger u. a. durch die Verwendung dünnwandiger Rohre mit grossem Durchmesser. Bei 10 × 0,5 mm ist allerdings das Biegen derselben nicht mehr trivial. Mit passenden Biegefedern geht es so »lala«, besser sind Rohrbiegezangen kombiniert mit einer strammen Sandfüllung. 8 × 1 mm oder 10 × 1 mm lassen sich hingegen mit Biegefedern gut in Form bringen. Eine Alternative sind immer Entwürfe mit weniger Biegungen und mehr Lötstellen.
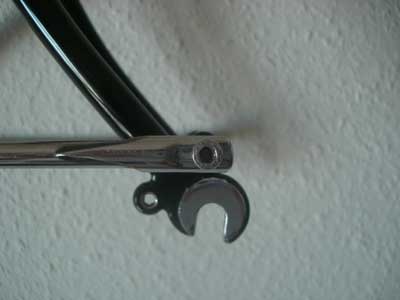
Ein weiterer Punkt ist das Material: Obwohl polierte Rohre aus rostfreiem
Stahl ja hübsch aussehen und auch die hässlichen, rostigen Scheuerstellen
wegfallen (vgl. Bild 3):
Muß es wirklich »Niro« sein?
Die Bearbeitung gestaltet sich mühseliger, Werkzeuge werden schnell stumpf
und:
Auch rostfreie Stähle unterliegen der Korrosion. Gerade die Legierung
1.4301, die sehr verbreitet ist und aus der auch Besteck und Spülen
hergestellt werden, reagiert empfindlich auf Salzlösungen. Tja, und die
Unterstreben sausen ganz schön tief über der Strasse durch den Salzwinter …
Andere Legierungen vertragen das besser (z. B. 1.4571), aber der Stahlhändler, der davon »mal eben« 3500mm in so exotischen Dimensionen wie 10 × 0,5 mm besorgen soll, wird sicher nicht begeistert sein.
Auch soll nicht verschwiegen werden, daß hochbelastete Lötverbindungen aus rostfreien Edelstählen zur Ablösung an der Grenzfläche Grundmaterial – Lot neigen. Ev. könnten da spezielle, besonders aggressive Flussmittel für rostfreie Stähle helfen. Besser ist es vermutlich, die Rohre per Schutzgasschweissung mit Elektroden aus identischem Material zu verbinden.
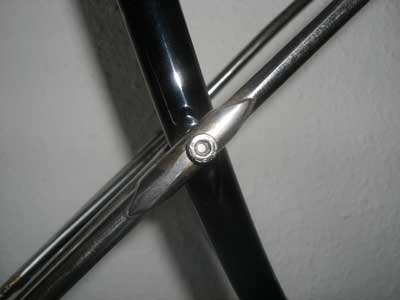
Insgesamt ist es aber für den, der im heimischen Bastelkeller den Lowrider neu erfinden möchte, empfehlenswert, eine unvergütete, nichtlegierte Stahlsorte zu nehmen (z. B. St. 37, es muss nicht 25CrMo4 sein). Die Verarbeitung (biegen, bohren, löten) ist einfacher, die mechanischen Eigenschaften ausreichend.
Und eins nicht vergessen:
Ohne 3-dimensionale »Fachwerk«-Abstützung sind oben genannte
Rohrdimensionen als alleinige, biegebelastete Unterstrebe zu schwach!
Fazit
Kritische KonsumentInnen kaufen keine Lowrider mit »Sollbruchstelle«!
Im Gegensatz zum hinteren Gepäckträger, wo eine Reihe einfacher Modelle zufriedenstellend funktionieren, sind viele auf dem Markt erhältliche Lowrider-Konstruktionen mangelhaft und bei hoher Belastung dementsprechend bruchanfällig. Besonders genau sollte man/frau sich den Bereich der Unterstreben-Verschraubung anschauen.
Neben der genauen Prüfung des Marktangebots bieten sich hier auch eigene Verbesserungen an, zu denen der Artikel einige Anregungen geben möchte. Für weitere Fragen steht der Autor via Redaktion gerne zur Verfügung, auch freuen wir uns über Berichte über eigene Erfahrungen mit den genannten Modellen.
Zum Autor
Stefan Buballa, Arzt, Alltags- und Reiseradler, Selbstbau eines Reiserades und eines Alltags-Kurzliegers. Er ist fasziniert von der Schlichtheit und ökologischen Effizienz muskelkraftbetriebener Fahrzeuge. Besondere Interessen: Ergonomische und leistungsphysiologische Aspekte. Besondere Schwächen: Radreisen in Afrika und Nahost …